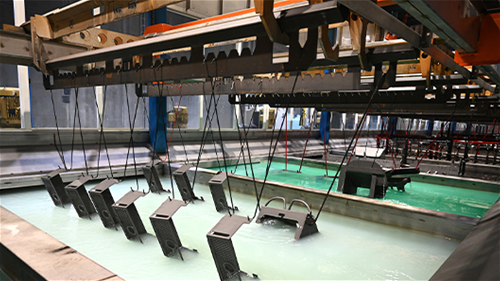
The SST® coating system is unlike any other system in the finishing business. Not only does it significantly reduce the amount of floor space needed, but it also allows increased load density. Modular construction allows for faster installation, and the automatic voltage control reduces paint costs. The PLC makes it easy to automatically lengthen immersion times and ensure proper coating thicknesses, as well as monitoring tank levels and oven temperatures. Therma-Tron-X SST® systems can handle high volume electrocoating, auto-deposition coating, powder coating, liquid spray painting, cleaning, pretreatment, and heat-treating operations with ease. From screws to truck bodies, SST® systems are designed to handle a variety of part sizes, weights, and complexities. Since the parts index is vertically in and out through each stage, immersion and spray treatments can be accomplished in tanks only slightly larger than the maximum work envelope. This greatly reduces tank charging costs, as well as minimizing water and utilities consumption. SST® systems are also fully automated, demand less floor space and require minimal labor to operate and maintain.