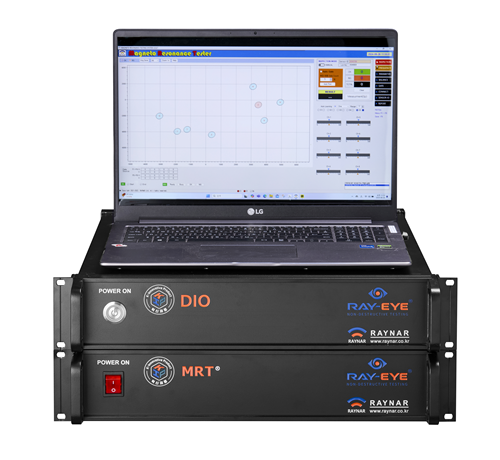
IN the ever-evolving world of quality control, Raynar has pioneering an innovation in non-destructive testing (NDT) technology: magnetic resonance testing (MRT). This innovation aims to redefine standards in pipe and tube production, offering precision in detecting internal defects that other methods might miss. MRT technology is an innovative method for detecting a wide array of flaws, including pit and line defects, which are crucial for maintaining the integrity of pipes during the production process. Unlike traditional NDT methods, which require multiple inspections for different types of defects, MRT offers a comprehensive solution. It can simultaneously detect cracks, assess heat treatments, inspect welding quality, verify screw taps and measure dimensions. This multifaceted capability not only saves valuable time, but also enhances the overall reliability of the inspection process. The versatility of MRT extends beyond pipe production. It is a vital tool for inspecting pipe hydrogen embrittlement, identifying structural defects, monitoring metal at materials and even detecting cracks in sintered powder metals. This broad applicability makes MRT an invaluable asset across various sectors, including energy, automotive and aerospace.
Raynar's MRT technology is also revolutionary for battery manufacturers. It offers an advanced solution for monitoring the welding conditions of aluminum terminals to copper plates - a critical process in battery production. The MRT welding inspection solutions distinguish between proper and defective welds by generating eddy currents at varying frequencies. This technique allows for an in depth evaluation of the junction's condition and bond strength, ensuring the highest quality in battery terminal connections.
MRT stands out with its array of distinctive features: • Real-time. non-destructive inspection: offers instant results without harming the metal, applicable to all metals. • Comprehensive defect detection: identifies cracks, voids, fine defects. surface roughness, stress discrepancies and dimensional inaccuracies. • Al-driven analysis: utilises advanced algorithms for precise internal flaw detection. • Patented non-contact sensing: ensures safety and efficiency with its global patented technology. Enhanced quality control: faciltates the detection af defects in welding, soldering and heat treatments. Data management: provides storage and statistical analysis of inspection data for improved quality assurance. • Remote operation: allows for unmanned tuning and management, streamlining the inspection process. Visitors can discover more by visiting Raynar's booth at FABTECH 2024, located #5766 and can experience how MRT is changing quality control and setting new standards in manufacturing.